Ore Tracking and Inventory Management
SGC Australia are integrators for world class control and optimisation supply chain solutions developed by Eka.
The Stockyard and Terminal Management systems consist of multiple modules which broadly include Anti Collision, Stockpile Management, Site Automation and Quality Management solutions.
The solutions have been adopted across major miners and agricultural exporters including at major export port terminals, storage sites, processing sites, and mine sites, and provide a multitude of solutions and commercial benefits, within a single software package.
Each module has been designed to be easily configurable thus reducing setup, testing and commissioning periods compared with traditional systems.
Each of the modules supports IEC 61131-3 open standard for programmable logic controllers and are capable of being deployed in a high availability clustered or load-balanced server environment using recommended Microsoft practices.
The modules are detailed within and collectively form the Insight CM product suite shown below.
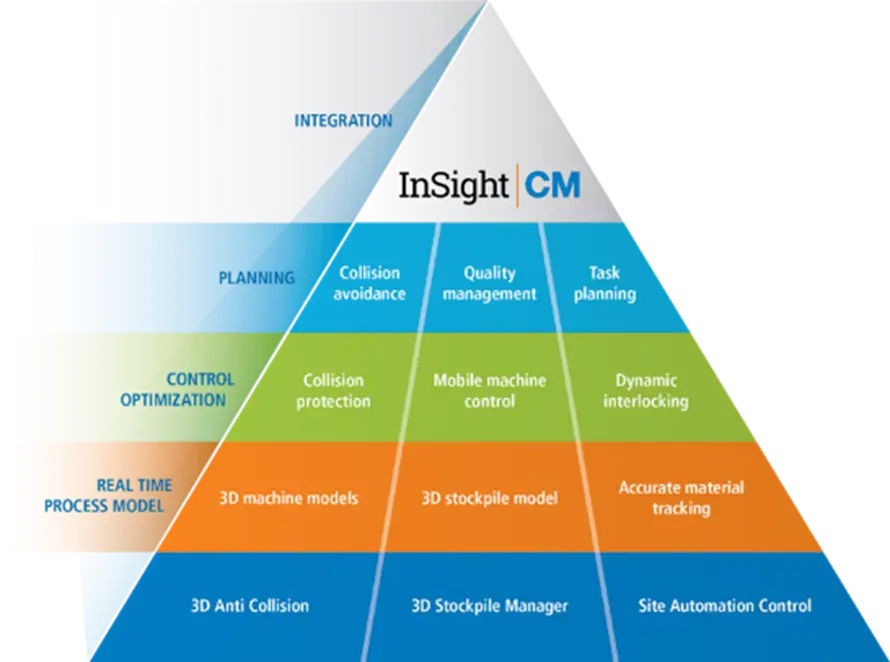
Insight CM
Delivered within a single platform, Insight CM, ensures all site operations are monitored and controlled via a single, fully integrated solution.
Insight CM provides better utilisation of site assets through the use of smart interlocking to control equipment based on product location, improved operational awareness and control through real-time product tracking, smart task control, and 3D visualisation, and real-time visibility into all operations including a comprehensive reporting suite for reporting and visibility of operations.
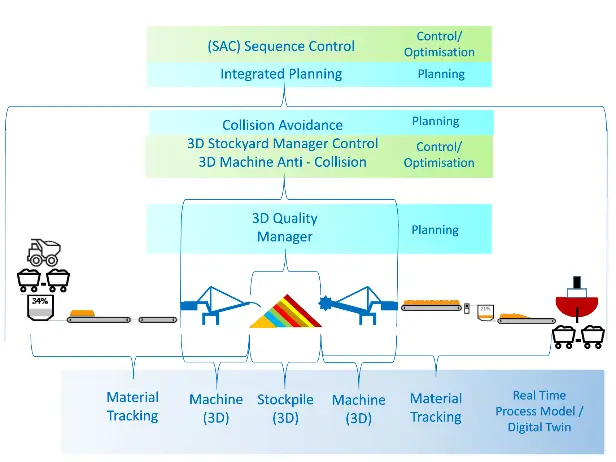
Stockpile Management System (SMS)
The Stockpile Management System (SMS) uses a stockpile model as the basis for the control of Stacking and Reclaiming within a stockyard. The model accounts for deposition and reclaiming of product in stockpiles updated from positional and weightometer information and integrates with tracked material movement throughout the plant.
Unlike traditional SMS systems, the Insight CM SMS uses a pattern based stacking and reclaiming system to dynamically control the mobile machines based on the current state of a stockpile. This flexibility ensures minimal configuration and commissioning time and simple control within the respective Field PLCs.
Key features and benefits
- Real time platforms coded and configured using open international architectures and best practices
- Integrated 3D site environment user interface
- Tight coupling with process controls to ensure accurate real-time measurement and modelling
- Interconnectivity to other systems based on industry standard and latest technology such as OPC UA and Web Services
- Use of accurate 3D stockpile modelling as the basis for control algorithms and optimisation
- Application of advanced deposition rate control and optimisation algorithms to take advantage of the 3D spatial awareness
- Allows users to configure stacking and reclaiming patterns to any shapes required by the business. This data can be saved against site scenarios and conditions such as weather/season and business focus like quality or throughput
- Allows the machine control systems to focus on machine control only
- Ensures consistent stacking results to maximise site space and throughput capability
- Incorporates advanced techniques like infill stacking and smart relocation
- Removes the need to continually carry out manual stockpile position and shape checks
- Improves business access for up to the minute and accurate process, inventory and (with QMS) quality information
- Provides the ability to visually display stockpiles to assist with informed planning and scheduling decisions
- Allows for advanced machine automation using existing site machines
- Apply automated stacking to part reclaimed piles
- Full stockpile history backed up to an offboard database.
- Allows modification to stacking patterns and pile shapes based on business and technical requirements
- Passive option availability for visualisation only
- 24/7 uptime and control system robustness
- Commercially backed and supported solution
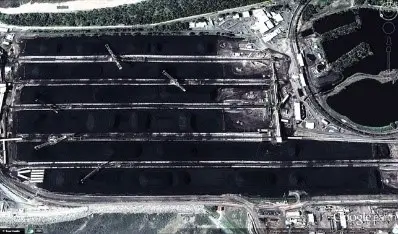
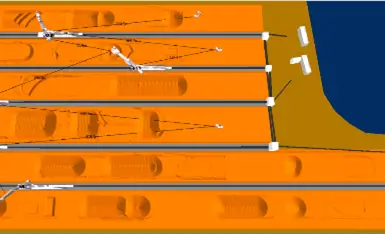
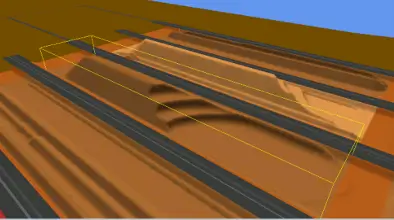
Site Automation Controls (SAC)
Site Automation Control is a dynamic site management and control system, incorporating high level process planning, scheduling, and product tracking features.
With Site Automation Control, operators can graphically view all assets, and effectively and intuitively plan receival, transfer, and loading tasks.
The system provides state of the art site management and control that improves product integrity, uniformity, and production efficiency, leading to a reduction in operating costs.
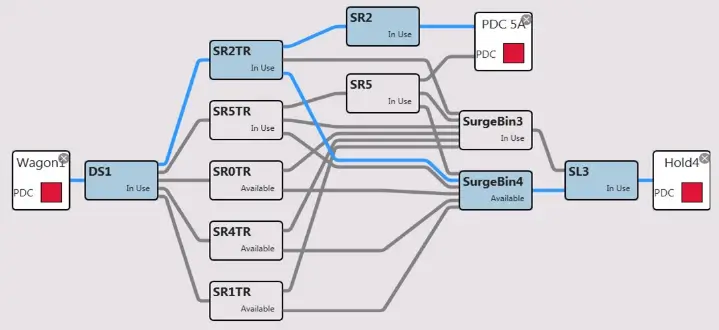
Key features and benefits
- Real time platforms coded and configured using open international architectures and best practices
- Detailed modelling capability including processing plants, surge bins, crushers and separators etc.
- Effectively manage your sites while saving money and improving margin
- Gain real-time visibility into all product movements and material quality, inventory and quality
- Allows for better utilisation of site assets by using smart interlocking to control equipment based on product location
- All site operations monitored and controlled via a single, fully integrated solution.
- Provides improved operational awareness and control through real-time product tracking and smart task control
- Provides Real-time visibility into all operations through a comprehensive reporting suite that provides complete reporting and visibility of operations
- Gives greater usability & flexibility including accurate and automated material tracking, blending control, quality management, power saving and utilisation efficiencies
- Improves source to destination task management
- Provides accurate and automated material tracking, blending control, quality management (with QMS), power saving and utilisation efficiencies, and the ability to pre- plan primary and backup operations and routes
- Integrated Planning tool to assist operations with up to date progress on the current plan.
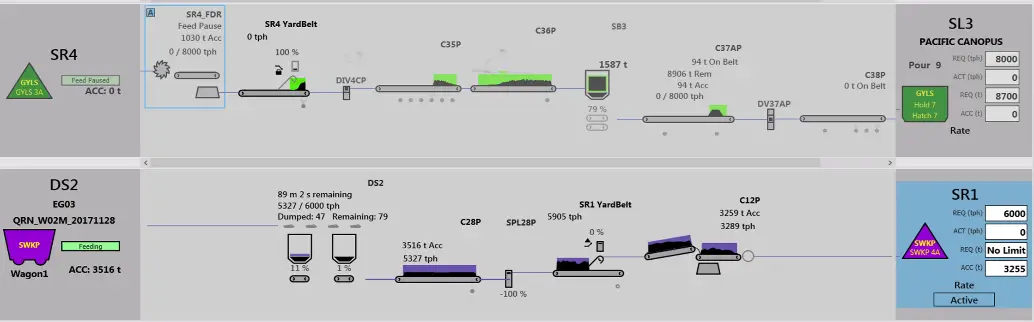
Quality Management System (QMS)
The QMS is designed to provide accurate and automatic volumetric modelling of the quality of material lots in real time, leading to confident prediction of contract deliveries and ensuring maximisation of margins, reduction in waste and reduced ‘out-of-quality’ penalties.
The QMS utilises the Site Automation Control (SAC) and Stockpile Management System (SMS) in 3D to ensure quality sublot information ceases to be an independent function that is considered and managed in isolation to the process.
Instead, quality becomes a closely integrated function to the movement of materials and provides the basis for decision making for future business processes.
Integrated Quality Management Systems (QMS) have been adopted by major global mining companies to manage their contract delivery, reduce penalties and maximise profit. Parcels of material can be monitored against customer specifications with tools provided to indicate when reclaimed parcels are out of specification.
‘What-if’ scenarios can be executed on a stockpile using different reclaiming operations within the reclaim planning tool to view the predicted aggregate quality of particular operations prior to actual task execution.
Key features and benefits
- Generates accurate and automatic 2D and 3D volumetric modelling of the quality material lots in real time
- Quality results are presented in real-time, meaning short term plans and variances from expected results can be actioned immediately when assay results are available
- Material quality is able to connect with physical material at greater granularity meaning that part reclaimed and filled piles have known calculated quality. As a result, production decisions are not constrained by the inability to understand delivery quality. Weighted average methods can become extremely inaccurate in these scenarios.
- Increase to quality prediction performance through the tightening of the quality envelope on delivered consignments through more accurate predictions
- Production increases due to decision making flexibility because material quality is included where part reclaiming, and refilling has taken place
- Considerable Business Improvement Benefits including accuracy, usability, and integration with planning processes and systems
- Risk mitigation by removal of dependencies on legacy systems and improved accuracy and redundancy through implementation of latest technology software.
- Confident prediction of contract delivery allowing maximising of margins and lower waste of valuable resources
- Reduced incidence of ‘out-of- quality’ specification events that significantly reduces the risk of penalties
- Integration with terminal planning functions to reduce risks associated with ensuring the right material is available to the right place at the right time. This reduces uncertainty and cost of logistics.
- Removes the need for manual update of stockpile shapes and locations. Exact, up to the minute status of stock and position is known and can be distributed to business stakeholders improving timeliness of decisions and mitigating risk of unplanned results
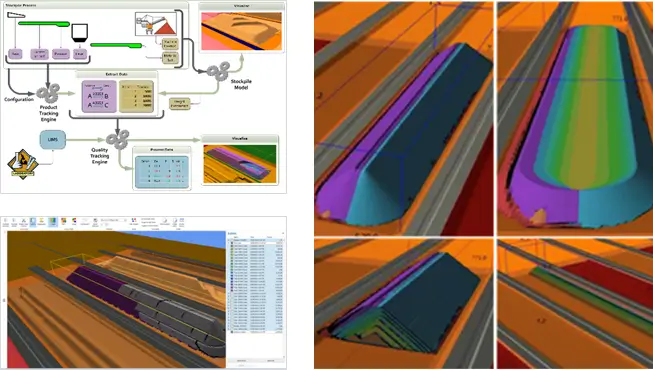
Anti-Collision System (ACS)
The Insight CM 3D Anti-Collision System (ACS) is a standard, commercial-off-the-shelf (COTS) product for the provision of machine-to-machine anti-collision protection for stockyard facilities.
The system provides protection against collision with other equipment and static objects within stockyard facilities and can include the protection of dynamically created user defined exclusion zones.
The system is fully configurable and scalable, allowing for the deployment, and protection of, machines and assets as they are commissioned and brought on-line as part of new stockyard installations, or as part of expansion works within existing stockyards.
An important feature of the ACS is the ability to prevent stockyard machines from moving into temporary protected areas known as User Defined Exclusion Zones.
These protected zones can be added and deleted to provide protection for work areas. The ACS provides full three-dimensional (3D) collision avoidance and a real-time 3D ‘fly-around’ user interface.
Key features and benefits
- The system is easily configurable and supports the direct import of 3D geometric models of permanent and temporary stockyard features including stockyard machines, fixed and temporary stockyard equipment and stockyard profiles
- All imported models are treated as 3D geometric shapes within the system. The x-y-z coordinates of each feature within the stockyard are referenced to the stockyard datum point.
- For dynamic objects (e.g. stockyard mobile machines) the machine long travel, slew, and luff axes positions are referenced from real- time machine position instrumentation.
- The system can directly interrogate GPS receivers using standard messaging protocols.
- The ACS supports industry standard open communication protocols.
- The system is readily scalable, stockyard machines can be easily added or removed via the configuration import process.
- The ACS calculates the true distance between 3D geometric objects. In the stockyard environment it allows for closer operation of machines whilst maintaining full ACS protection distances.
- The ACS can also protect against mobile vehicles such as Trucks and Dozers whereby rail mounted machines will halt if there is potential for collision.
- The ACS evaluates the machine-to-machine separation distances and generates control actions based on configurable protection zones.
- The ACS supports a wide range of functions for isolated machines or machines identified as being in a degraded or off-line state due to communication failure or position instrumentation failure.
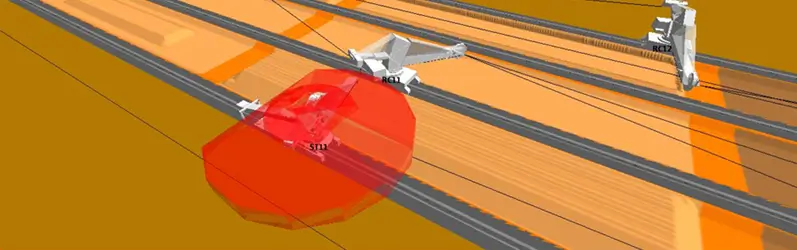
Commodity Site Manager (CSM)
The Commodity Site Manager (CSM) System is an end-to-end solution to manage the physical movement of commodities.
Inventory Management
Track and manage both physical and owner stock inventory of commodities, including storage locations, quantity and quality.
Supply Chain Management
Manage the flow of commodities from production to consumption, including logistics, transportation, and delivery via Ship, Train and Truck.
Analytics and Reporting
Extensive in-application reports and customisable dashboards, to perform data analysis and support business decision-making.
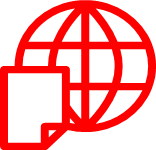
Collaboration and Communication
A platform for communication and collaboration with suppliers and clients to support efficient and effective supply chain management.
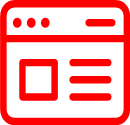
Compliance and Regulatory Management
Tools to manage compliance with local, state and national commodity specific regulations.

External Systems Integration
Supports Web API integration with external systems, such as ERP, accounting, and CRM, to streamline operations and improve visibility.
Typical CSM architecture consists of a remote, centralised head office production server and multiple remote site server deployments (as required). The remote site databases manage local stock transactions (i.e. local grain movements at a terminal or receival site) and are automatically synchronised with the head office database for centralised storage and management of enterprise
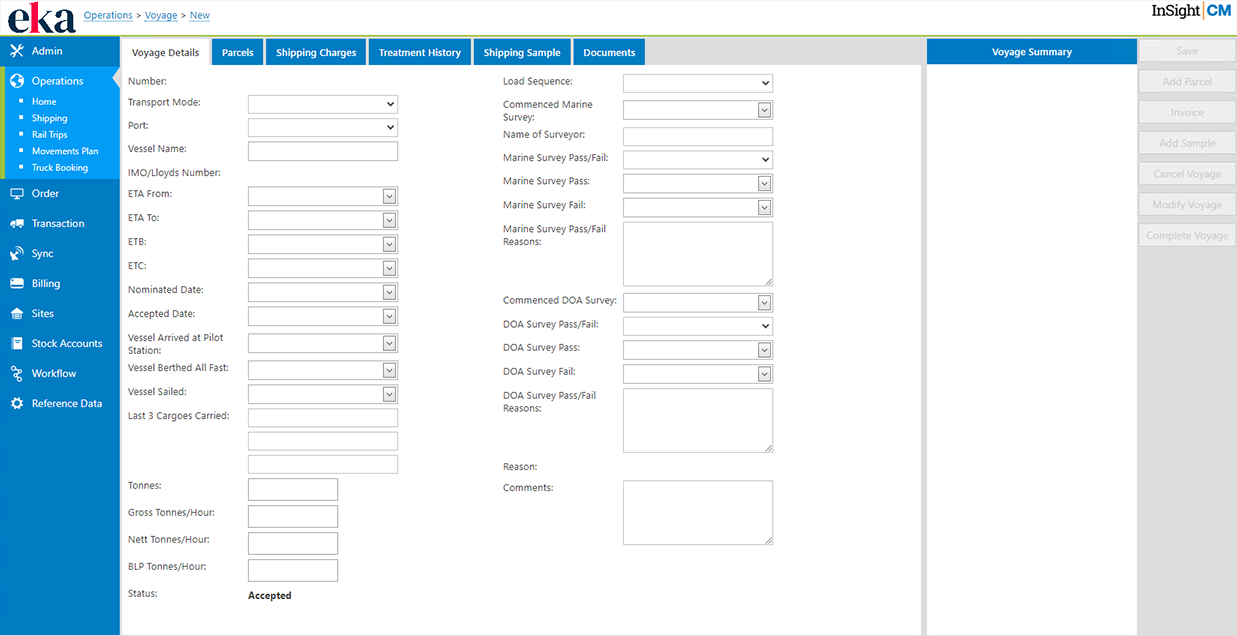
CSM features include:
- Real-time Inventory Tracking
- Quality Management and Planning Tools
- Product Ownership Tracking
- Orders and Billing Management
- Integrated Charges and Invoicing
- Forecasting and Demand Planning
- Web API for External Systems Integration
- Customisable Workflows
- Multi-site Inventory Management
- Reporting and Analytics
- Secure Authentication and Authorisation, and
- Audit Trails
Functional components of CSM can be broken down into the following categories:
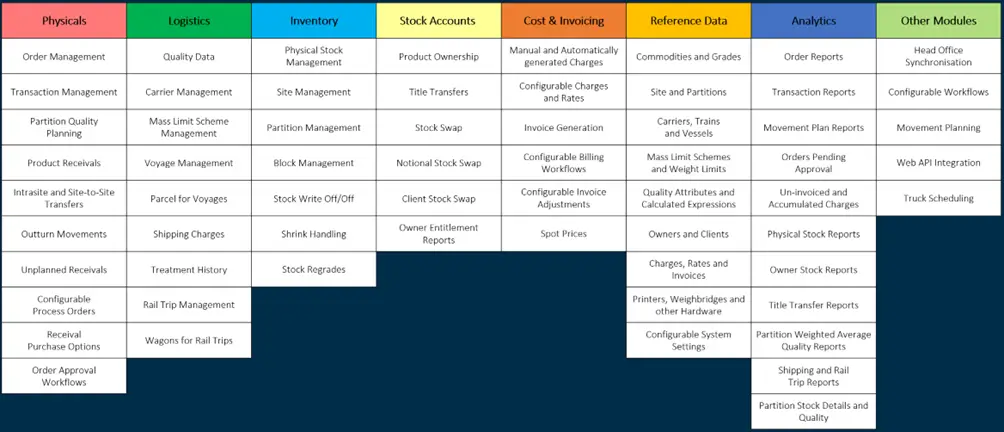
High quality solutions without compromise
Benefit from our demonstrated experience and success. Get in touch to explore how SGC Australia’s multi-disciplinary expertise can positively impact your operations.